Just How to Make Sure Compliance When Utilizing Chemical Products in Your Operations
Just How to Make Sure Compliance When Utilizing Chemical Products in Your Operations
Blog Article
Key Considerations for Choosing the Right Chemical Products to Attain Reliable Integrated Solutions in Your Procedures
Choosing the proper chemical products for integrated services in operations needs a diverse technique that encompasses various vital factors to consider. From analyzing chemical compatibility to making certain adherence to regulatory criteria, each aspect plays an essential function in enhancing operational efficiency and safety and security.
Recognizing Chemical Compatibility
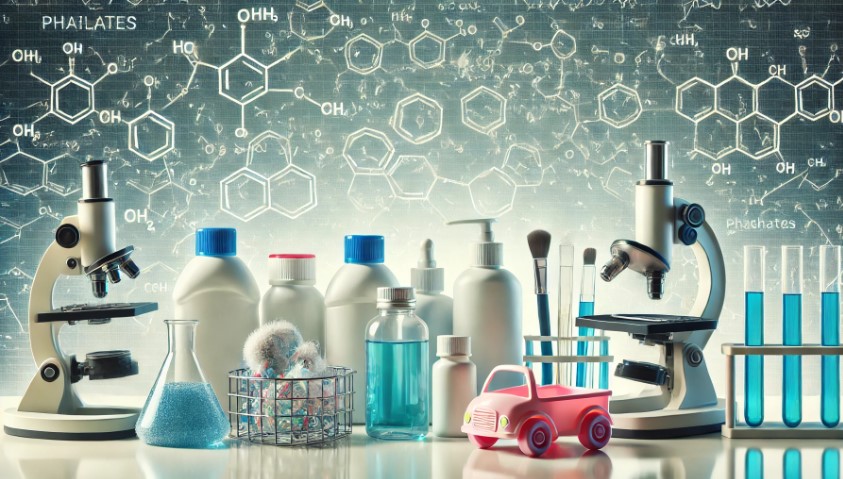
To examine compatibility, one should think about variables such as the chemical buildings of the substances included, consisting of pH, focus, temperature, and the presence of contaminations. Making use of compatibility graphes and data sources can provide useful understandings right into possible communications. Additionally, performing small-scale examinations can aid identify unanticipated responses that might not be recorded.
Elements such as moisture, light exposure, and temperature level can influence the security and reactivity of chemical items. By prioritizing chemical compatibility throughout the choice procedure, companies can boost operational performance, reduce the risk of crashes, and guarantee conformity with safety procedures.
Examining Regulatory Compliance
In the facility landscape of chemical item selection, reviewing governing compliance is vital to ensuring not only security yet additionally legal adherence. Organizations should browse a myriad of guidelines, from local and national laws to worldwide requirements, that regulate the use, storage, and disposal of chemical substances. This calls for a complete understanding of applicable regulations such as the Occupational Safety and Health Administration (OSHA) standards, the Environmental Security Agency (EPA) guidelines, and the European Union's Registration, Evaluation, Authorisation and Limitation of Chemicals (REACH)
When choosing chemical products, it is vital to confirm that providers offer Security Information Sheets (SDS) that detail prospective hazards and handling needs. Businesses must verify that the chemicals comply with industry-specific laws, which may enforce additional specifications. Non-compliance can result in severe charges, including fines and functional shutdowns.
In addition, organizations need to stay upgraded on regulatory modifications, as non-compliance can arise from out-of-date techniques. Establishing a durable compliance approach, consisting of regular audits and worker training, can aid guarantee adherence to present laws. Ultimately, prioritizing regulative conformity not just reduces danger however additionally boosts the company's track record and functional performance.
Assessing Environmental Influence
Exactly how can companies effectively evaluate the environmental effect of chemical products during the selection process? Organizations ought to begin by recognizing the prospective hazards connected with each chemical, including poisoning, determination in the setting, and bioaccumulation potential.
In addition, companies can take advantage of third-party qualifications and eco-labels that indicate compliance with ecological standards - Chemical Products. Engaging with vendors that prioritize sustainability practices can also boost the selection process. It is critical to assess not just the straight effects of chemical usage however likewise the indirect impacts, such as energy usage and waste generation
Applying life process assessment (LCA) methodologies can offer detailed understandings right into the ecological impact of chemical items, highlighting areas for renovation. By prioritizing transparency and partnership with stakeholders, companies can make enlightened choices that straighten with their read this article sustainability objectives while decreasing adverse ecological end results. This aggressive method inevitably promotes Read More Here a much more responsible and eco-conscious operational structure.
Examining Cost-Effectiveness
While reviewing chemical items for operational usage, companies should also take into consideration cost-effectiveness as a vital element in the option process. This involves examining not only the initial acquisition cost but likewise the total expense of possession, which includes factors such as usage performance, maintenance, and disposal prices. Chemical Products. A product that shows up low-cost upfront might incur greater prices in energy usage or need even more frequent substitute, inevitably impacting the bottom line
In addition, organizations must assess the possibility for price savings through optimized formulas that boost efficiency and reduce waste. As an example, products that require reduced application rates or offer faster processing times can result in significant savings gradually. It is also necessary to think about the effect of regulative compliance costs, as non-compliance can lead to fines and increased functional costs.
Moreover, organizations should review the lasting value originated from the chemical items, consisting of improved top quality, enhanced productivity, and boosted security. An extensive cost-effectiveness evaluation equips companies to make enlightened decisions that straighten with both their monetary objectives and operational purposes, ultimately bring about sustainable and reliable practices.
Identifying Distributor Reliability
Distributor reliability is extremely important when choosing chemical items for operations, as it directly affects both item quality and functional efficiency. A trusted provider consistently provides top quality products promptly, ensuring that your processes stay nonstop. To determine supplier reliability, begin by examining their online reputation within the industry. Look for testimonials, testimonials, and study that highlight their performance and customer complete satisfaction levels.
Following, consider the distributor's background of compliance browse this site with regulations and criteria. A reliable distributor ought to have a robust quality control program that abides by industry guidelines. In addition, examine their ability to supply technical assistance and item info, which is critical for informed decision-making.

Final Thought
In conclusion, picking the ideal chemical products for incorporated remedies requires an extensive evaluation of numerous important elements. Recognizing chemical compatibility, making certain regulative conformity, evaluating ecological impacts, assessing cost-effectiveness, and determining dependable distributors collectively add to informed decision-making.
Report this page